We can't find the internet
Attempting to reconnect
Something went wrong!
Hang in there while we get back on track
What I Learned from Working at 6 Fulfillment Companies in 3 Months with Channa Ranatunga
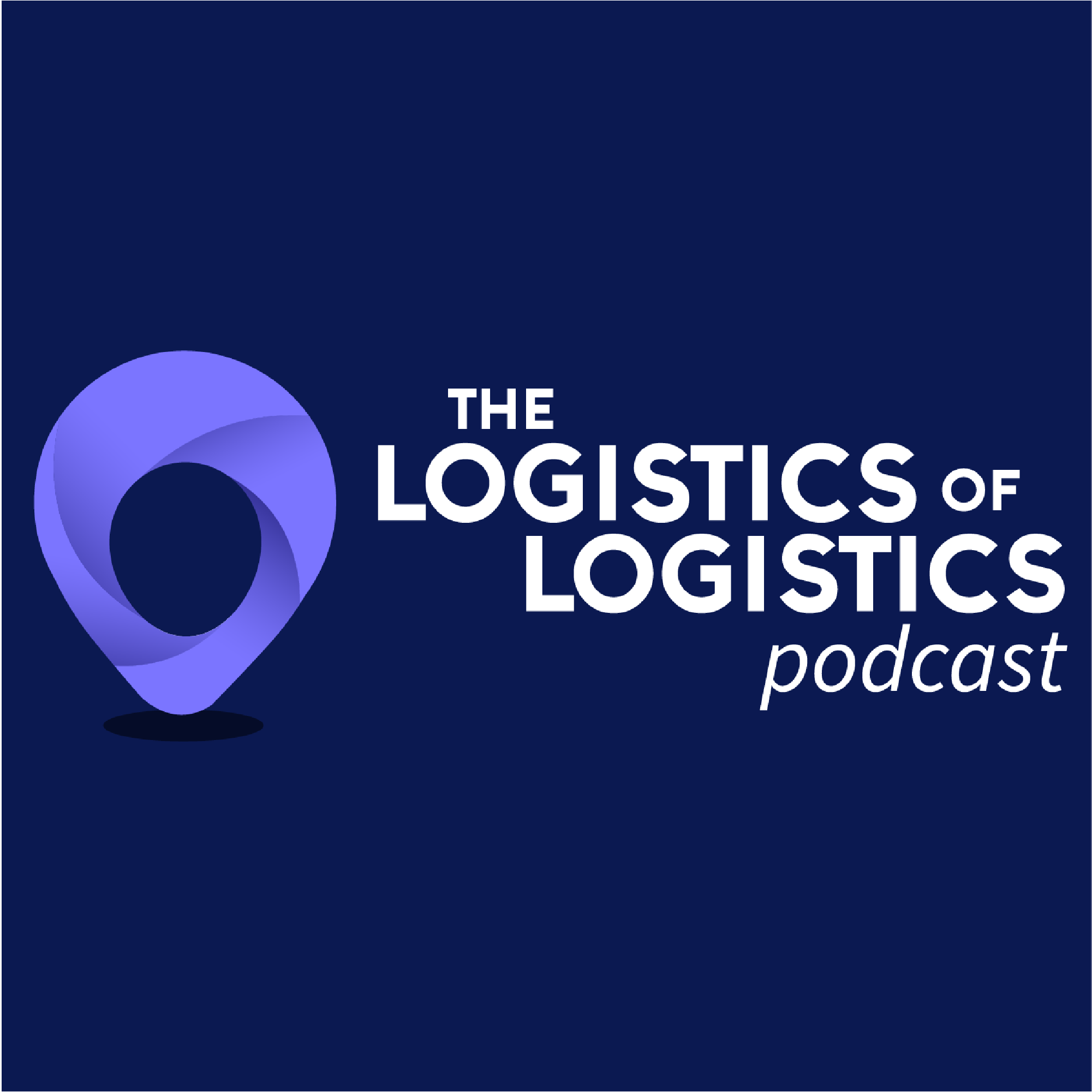
Access AI content by logging in
What I Learned from Working at 6 Fulfillment Companies in 3 Months with Channa Ranatunga
Channa Ranatunga and Joe Lynch discuss what Channna learned from working at 6 fulfillment companies in 3 months. Channa’s company, Rabot provides tools that enable improved worker efficiency in fulfillment warehouses, so he wanted to gain firsthand experience working in fulfillment.
About Channa Ranatunga
Channa Ranatunga is the Co-founder and CEO of Rabot, a technology company dedicated to building smart tools that reduce repetitive work and improve worker efficiency in warehouses. Channa is an experienced entrepreneur in the logistics and supply chain space. He enjoys learning about new technologies and current challenges faced within the warehousing and fulfillment space and is always looking to connect with logistics professionals. Prior to starting Rabot, Channa was a Senior Applications Specialist at a machine vision company. Earlier in his career, Channa owned a pack and ship store and also founded a wireless device company focused on smart farms.
About Rabot
Rabot builds smart tools to reduce repetitive work and improve worker efficiency in warehouses. Due to the growth of e-commerce in the global economy, e-commerce fulfillment and logistics companies are struggling to maintain profit margins as their customers expect shorter and error-free fulfillment cycles. This is prompting the need for smarter technology solutions to help with the rapid growth. At Rabot, we are building smart tools to reduce inefficient, inaccurate, and repetitive manual work and improve warehouse operations' traceability. Rabot is based in Arlington, Texas.
Key Takeaways: What I Learned from Working at 6 Fulfillment Companies in 3 Months
Channa learned the following from working at 6 fulfillment companies in 3 months:
- People
- The workers are generally very hard working.
- Diverse workforces, usually a family environment.
- Many workers are fearful of robotics because they see it as a potential threat to their jobs.
- Many workers are struggling financially, some sad stories, people living in cars.
- High turnover, repetitive work, demanding physically, no sick days.
- Workers often work in the gig economy, very interested in Uber, Lyft, etc. as alternative sources of income.
- Management was typically very kind, treated people well.
- Everybody, management, and workers are trying to do the right things.
- Process
- The work is repetitive, sometimes difficult to stay focused, which leads to quality issues.
- Some processes work well, easy to manage, and do a good job, other processes are very hard because there is no technology or the tech is mismatched or inadequate
- In general, too many manual processes, writing out barcode numbers on to paper, etc.
- Management often don’t have visibility into the process – only the output
- Management’s lack of visibility into the process, means there are errors, bad orders
- Process variability based on the operator (experience, effort, training, size/strength)
- Technology
- Many fulfillment companies are not using technology properly.
- Some warehousing and fulfillment company not utilizing any technology at all.
- WMS not used in two of the six fulfillment companies – manual processes, no scan guns.