We can't find the internet
Attempting to reconnect
Something went wrong!
Hang in there while we get back on track
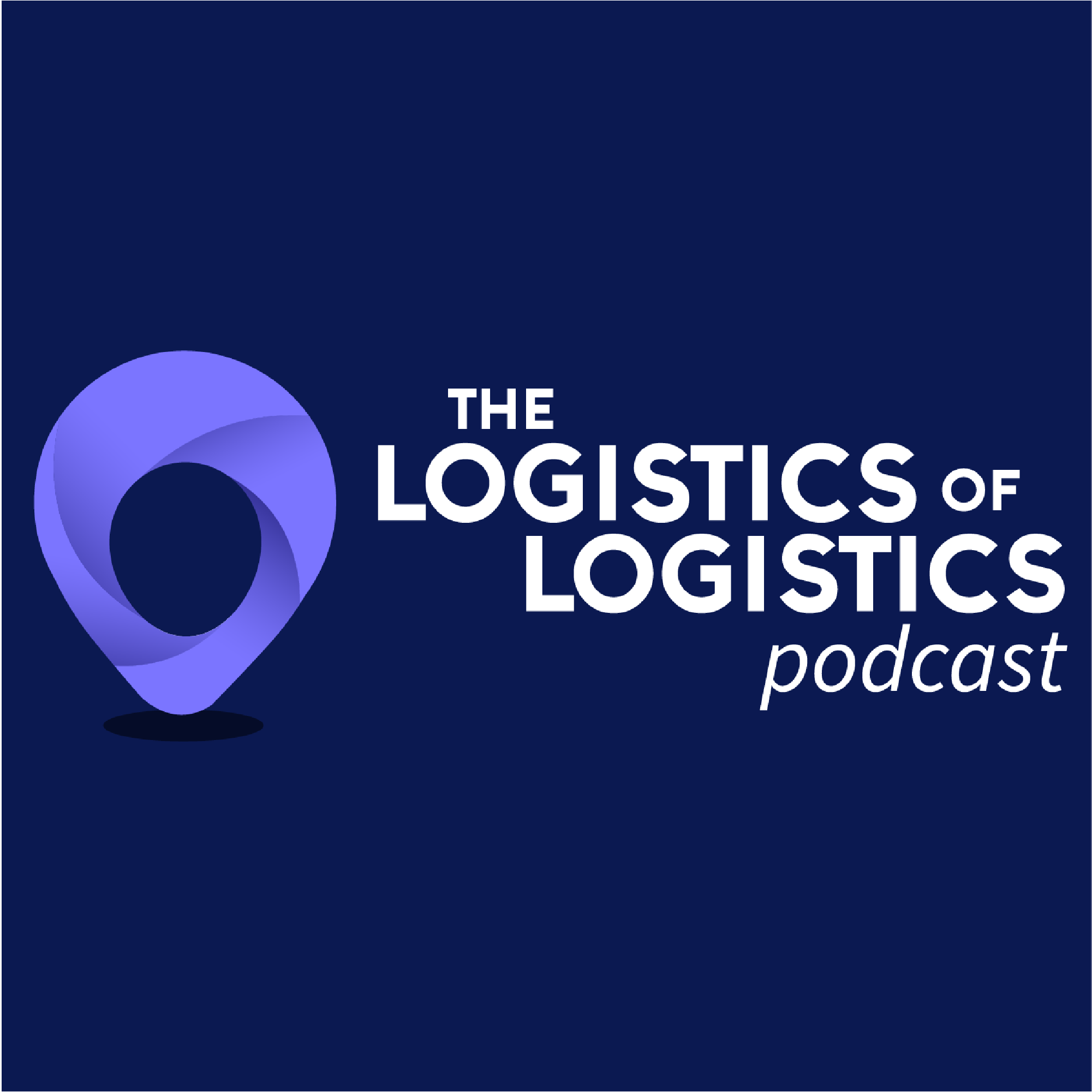
Access AI content by logging in
Want to know how you can deploy a smart warehouse for your business? Today’s guest is Dan Gilmore of Softeon, a company that provides a full suite of flexible and robust end-to-end supply chain software solutions to deliver success. He joins Joe Lynch to talk about the idea and technology behind their system. They discuss some of the big trends impacting warehouses, e-commerce, and retail. From labor shortages to automation, Dan enlightens on the benefits of WMS and WES for any business. Tune in to better understand the perks of this new smart technology for optimizing your business!
The section below is transcribed. Transcription has limitations so there may be grammar and typo issues.
The Smart Warehouse With Dan Gilmore
Today's topic is the smart warehouse, with my friend, Dan Gilmore. How's it going, Dan?
Great Joe. Very happy to be here today.
Yes, I'm glad I'm finally getting to interview you. Dan, please introduce yourself, and your company, and where you're calling from today.
Yes, again, Dan Gilmore. I'm chief marketing officer of a supply chain software company called Softeon. We'll get into that maybe a little bit more in just a second here, but company's headquartered in Reston, Virginia, just outside Dulles Airport. I happen to be in the Dayton, Cincinnati, Ohio area. Buckeye through and through, so go Bucks.
Why, I got to say go Blue now. Man, you dragged me down. Anyway, Dan, what does Softeon do?
Sure. Well, again, it's a supply chain software company, primarily supply chain execution. The company was founded in 1999, first customer all the way back then was L'Oréal, and just proceeded to build out a suite of solutions, very broad and deep capabilities. That includes warehouse management systems, as I said, that all the stuff that kind of goes around warehouse management systems. People package those differently, but things like labor and resource management, slotting optimization, yard management, and those kind of tools. And then a newer thing, which we'll get into today because it's so critical to what's happening in terms of the smart warehouse, is something called warehouse execution systems, which have been around for a while, but really gained prominence the last couple, three years, as a way to optimize and orchestrate order fulfillment level at a capability that's just beyond even very good tier one WMSs like Softeon has.
And then the category of stuff called distributed order management, which has to do with the optimal sourcing of product based on customer commitments as well as network capacities and constraints, and how do I get the lowest cost alternative that meets the customer needs, very prominently in omnichannel commerce. It's almost essential in retail, but we have a lot of B2B type successes in distributed order management as well. So there's some other things, but that gives you a pretty good flavor of what we do.
You guys started well before eCommerce was a thing, so you still support stores and that kind of warehousing?
Sure, so I mean, in addition to traditional WMS type capabilities, and for retailers, that would largely was store replenishment, now moving in obviously to eCommerce fulfillment, but many retailers are also looking to have a lot of activity at the store level, whether that's buy online, pickup in store, curbside pickup, or store fulfillment, so we've got some solutions there, both in terms of the distributed order management that I just referenced a second ago, is the tool that's going to say, "Hey, the best place to fulfill this order from based on the time commitments as well as inventory availabilities, labor availability, et cetera, is store three, four, five, six, seven," and then have the ability... So first you identify where is the right location, and that could be obviously a DC or a third-party facility or something like that, but the first word is the best place to source it from, and then if it's a store, we have a store module that facilitates the inventory transactions, and the picking transactions, and the shipping at a store level.
Yeah. That became a thing. I mean, I know, I think Target's one of those companies that delivers a lot... If you buy something online from them, they're more likely to ship from their stores these days.
Yeah, if it's a huge... I've seen a figure. I don't know, and it keeps rising.
The whole market has changed. The more high-tech feel and touch, the less back-breaking work and less bending over and lifting heavy cases.
It’s like 80% or 90%.
Yeah, I was going to say around 80%. That's the number I had in my mind too, that they're doing it from stores, which is rather incredible.
Yeah. Well, before we get into all of that, tell us a little bit about you. Where'd you grow up? Where'd you go to school? And give us some career highlights and bullet points before you joined Softeon.
Yeah, sure. Again, I've been pretty much, except very early in my life, an Ohio guy, my whole life. I grew up in the Akron, Cleveland area, and then got a job with NCR after grad school. I got an MBA from the University of Akron and I got a job at NCR, that was here in Dayton. I was a project manager, kind of in charge of barcode and data collection, and the way serendipity just kind of works, I moved from barcode data collection systems, and wireless systems, and then got into WMS, and was into consulting for a while, so I actually have done a lot of marketing in this space. I was also a chief marketing officer at RedPrairie before it got acquired by JDA and became ultimately Blue Yonder, but earlier in my life, I spent a couple of years implementing WMSs, a couple major projects down there in the Cincinnati area that really helped me learn a lot about how the technology actually works, and what's good, and what's less good. Notably, in 2003, I started a publication called Supply Chain Digest, which changed the face of online supply chain and logistics, news, and coverage. I still keep a light hand on it. I still write a column once a week still for Supply Chain Digest.
Yes. I know I have read that. It's funny. I did a lot of blog posts in the past, so when you are a writer, I joke I might research a little different than a professor's research. I Google, and you start to realize which publications have good content, because I'm a blogger. The bar's a little lower for a blogger than it is for somebody writing in a publication, and I would just go, "Man, oh man. This is a good..." Supply Chain Digest always had good stuff, so anyway. When and why did you join Softeon?
Yeah, it's been about four years now, and I had done actually a little bit of side consulting with Softeon before joining, and was just impressed with two things, first off just the breadth and depth of the software and a number of innovative capabilities, but just as important as that, I mean, there's a lot of companies that got good software. We think we've got bleeding edge software, but a number of companies out there. But really just the approach to customers and success, so I've never seen a company that consistently put its own interests behind those of its customers on a regular basis, and was just not going to let anything get in the way of a successful implementation, and that's really a track record that's unequaled in the marketplace, so just the care and concern for success at the customer level, and not looking at everything through a lens of how many professional services hours I can sell or something like that. It's really just kind of a different attitude, and that really intrigued me, and plus the company needed some help in the marketing area to get that message out, so a combination of those factors led me to join Softeon.
Excellent. Well, today's topic is the smart warehouse, with my friend Dan Gilmore. Obviously, things have changed quite a bit in this business, so talk about some of the big trends that are out there, that are impacting warehousing, and eCommerce, and retail. It impacts everybody
And these, most of the audience is going to say they're living these, so you know, it's not like these are big surprises, but it's still kind of nice just to put it all in context. Obviously, the growing distribution and labor shortage and there’s a shortage and manufacturing. Very acute, and everywhere you go, that's what you hear about, and just the turnover levels, and the retention, and just unprecedented, even with the wages rising substantially, so that's everyone's concern. That is naturally... And actually, after about a decade of very flat wage growth in warehousing and distribution until a few years ago. Now all of a sudden, of course the costs are taking off. I mean, Amazon is over $20 an hour with attractive signing bonuses. In many parts of the country, maybe a couple, three months ago now.
With parental leave for 20 weeks. I saw it on TV yesterday.
Is that right, now? I did not know that. That would be a very attractive benefit, and that's the advantage. And then Target, maybe two or three months ago, announced that they were raising their wage, in both stores and distribution centers, in some markets, not all markets, but in some markets at $24 an hour, and you think, "But that's $48,000 a year," so... And assume there's probably some overtime in there, right? Whatever, so a husband and wife, I'm just making up an example there, working at a Target DC in those markets, they could be pulling in $100,000 a year for a family, which is not bad money.
[caption id="attachment_7940" align="aligncenter" width="600"] The Smart Warehouse: With the e-commerce-driven cycle time pressure, it's unbelievable how fast you can get products these days.[/caption]
If I could add something into that, Dan, I think also... And this has come up on my podcast a few times. If I had a choice right now... I'm getting too old for that kind of work, but... I can't walk 10 miles a day. I think we needed to make that job easier, and we're going to get to that, because this is what the technology does, but I think it also makes the job more attractive, when they can say, "I go to that job, and I'm learning all this cool technology," as opposed to, "I'm just a strong back." If you can bring somebody in, there's a different feeling when I get to wear all that high-tech gear, and use high-tech systems, and say, "I'm part of the supply chain," as opposed to, "I'm just a strong back, and I walk five miles a day, and nobody gives a damn about me."
Yeah. There is no question about that, and I think both in terms of just a shortage of labor, and second just the ability to attract people into this career now, it's just the whole market has changed. I think that more high-tech feel and touch, and less back-breaking work, and less bending over, and lifting heavy cases, and all the kind of things that [inaudible 00:09:32] for a long time. I think you're spot on on that dynamic.
And if we do have a shortage, that means the people we do have have to be more efficient, and the way they can be more efficient is with tech of course, and we'll get into some of that in a minute, but... So that's one big trend that's going on. What's another big trend that's happening?
Yeah, well there's a bunch, and they're kind of interrelated as well. Obviously, the eCommerce-driven cycle time pressure, so obviously it's led by Amazon over your tablet, it’s unbelievable how fast you can get products these days, even somewhat obscure products. Not that long ago, I needed a new power cord for my HP computer, and somehow, Amazon was able to deliver that the next day. I'm like, "How do they have this cable someplace that they can get it to me in one day?" I think of all the thousands and thousands of cables that are out there, and they've got mine. So the cycle time pressure, and that both is in terms of getting the order processed from when it drops into the DC and out the door.
Obviously, companies are also moving distribution facilities closer to the customer, so the transportation part and parcel part of the journey is cut down as well. I mean, I can't remember the specific numbers, but I think it's Home Depot is building 170, 180 different of these local fulfillment centers that are being the largely cross-stock type of facilities that bring bulky items in and get them right to the customer in addition to the big giant warehouses that they already have. It's a fact of life. Eventually, we will teleport or whatever the product from the warehouse because it seems like we are reaching the Laws of Physics there that it can't be here any faster but maybe we will find a way.
I remember probably five, seven years ago, I was working on a digital marketing project. I was helping this distribution center, nice good size in Chicagoland, Peoria, and they said, "We're one-day shipping to 65% of the population of the US," and that was always what Indiana, and Illinois, and I guess there's so many DCs down in Ohio, could always make that claim, and that was good enough. So if you said, "I have a DC in the Midwest that can get me to the East Coast, and I have one out West," and that was good enough. We're not seeing that anymore.
Yeah. I mean, we're going to get to increasingly where same-day delivery just becomes a fact of life, and rather incredible, and you've heard Amazon and others talking about getting it down to two hours, or 30 minutes, or whatever again.
Well, that's what Target's doing with those DCs. I mean, their DCs are their stores, and we think we'll get to Walmart doing some of the same.
No question.
So, what's another trend that you're seeing out there?
Yeah, well just because obviously we're calling this the session, we're going to talk about the smart warehouse of the future, that's largely here today, but we've got smart everything, right? We've got smart houses, we've got smart cars, we've got smart refrigerators, we've got smart toothbrushes even. I saw that a couple years ago. I'm not sure if it's exactly taken off or not, but monitoring how often you brush your teeth. But what has that really meant?
Well, primarily, it's just talked about internet connectivity and sort of some kind of analytics around it, so you know, easy example is John Deere, or Caterpillar, or companies of that kind, putting sensors and other IoT-type devices on their equipment out in the field, so they can get a sense for how people are actually using it. They can do predictive maintenance on it. They can say, "Hey, your guys aren't using the equipment as effectively as they could if they change their techniques," or et cetera, et cetera, so I think it's certainly timely, and if we're going to have all the smart things, it's time for the smart warehouse too, but as we'll get into for the rest of the broadcast here, it's a lot different than just plain more internet connectivity, and sensors, and things like that. That can be part of it, but it's just a small part of it.
But the bottom line of it is, we are entering a new era of warehouse software technologies that are in fact much smarter than we've ever had before, and I've argued publicly for a couple, four years now, that we really had about 20 years of relatively incremental progress in WMS technology. I've used this in speeches before, but a few years ago, I pulled out of cleaning up my office around the holidays, as I often do, and I found an RFP from a major food company for a WMS circa 2003. I looked through that, and I thought, "You know what? This doesn't look all that different than the RFPs we're seeing in 2019, or 2020," or whatever year I was looking at that.
Really, the big difference is I looked at it, I said, "The big difference is not in the functionality being asked for." It's just that today, a lot of that functionality is in fact core product, configurable product, whereas back then, maybe a lot of it had to be achieved... more of it had to be achieved through customizations. I think that's probably true, but the fundamental way a warehouse operates, WMS operates, didn't change all that much from give or take 2000 to 2020, or somewhere in that kind of a range. But now with the smart technologies that we're talking about, they are brought in to bear by the warehouse execution systems, working with WMS I talked about before. This is a new ballgame, and it's going to be a fun for the rest of the discussion here, to talk about that.
So you threw in a new term there. You said warehouse execution system, and I know you said those have been around for a while, but they're now becoming kind of the norm, did you say?
Just becoming very prominent, and the value's starting to be recognized.
What is it?
They came about actually a good while ago from a couple, three companies really, that had the belief, and I think correctly so for most WMSs, that the WMS systems did not care enough about equipment throughput and utilization, so you wound up with big peaks and valleys. Now, anybody who's been in a distribution center, even a really busy one, you've seen it where there's all kinds of activity at the beginning and the middle of the wave, and then as the wave starts to dissipate, even on a big, expensive, huge sortation system, you've got a relatively small number of boxes moving around, waiting for that wave and everything to close out.
When you say wave, does that mean the orders come in waves?
Yeah, the work is released in what are called pick waves, and that's based on any number of different attributes. It could be the carrier schedule, or value-added processing that needs to be done, or just workload balancing across different pick areas of the company, so you organize the work against various attributes that constitute a block of work, that's typically referred to as a wave.
Yeah, so the problem is that I know I've got all these trucks that are going to show up, and they're taking different orders, so maybe I'm working to that order that's going to fill up that truck, or orders that are going to fill up that truck, and the problem is, to your point, is we've got already maybe a shortage of head count in there, and now when we have waves, now I'm not being efficient, because I've got too much work at one moment and then not enough in another.
Yeah, and the whole goal of WMS, and what we're going to talk about today with the smart warehouse, is really overcoming... I mean, obviously you've got to plan and execute based on the workforce that you have here today, and we'll talk about that.
So just having a warehouse management system that gives me stuff was great in the past, but you're saying, "I'll help you with a WES," or warehouse execution system. "I'm going to help you manage the flow.
Manage the flow of work and the resource utilization, so that's exactly right. In and just new ways. Part of that still ties into that interest in level loading or making the flow of goods across an automation system more smooth and consistent, because if you can do that, a couple things. First off, the total throughput of the system is likely to be better, and second, if it's a new facility, you could actually probably get by with a smaller sorter, if you will, because you're going to be able to utilize that sorter more consistently over a block of time, a shift, or however you want to look at it there. And the other kind of breakthrough that Softeon has had is that WES, while it has its roots in that level loading of the automation and better utilization there, the WES works extremely well even in non-automated facilities or lightly automated facilities.
[caption id="attachment_7941" align="aligncenter" width="600"] The Smart Warehouse: The fundamental way a warehouse operates didn't change all that much from 2000 to 2020. But now, with smart technologies, this is a new ball game.[/caption]
As a matter of fact, one of our leading customers, I'm not sure I can say their name, so I'm not going to, but actually did a press release a couple years back that talked about a 50% productivity gain from implementing WES, warehouse execution systems, on top of an existing Softeon WMS, and doing that in a totally manual environment, because everything is part of a system, right? You can have a sortation system, or you can have a goods divergence system, or put wall system, or whatever. It's got a certain capacity, certain throughputs, inputs and outputs, whatever. Well, 20 workers walking around on a three-level case pick module, they're a system too, and they have inputs and outputs, and throughput, and expectations, and all that. You know, the one big difference is that with a more manual system, you can actually throw more bodies at it, and up to a point of diminishing returns, gain throughput from that area, whereas a heavily automated system, kind of its rate is its rate, and you're not going to do a whole lot to affect that.
But this is what it... When you mentioned throughput, I mean throughput is everything, whether you're a plant, or whether you're a freight broker, or whether you're a warehouse. The stuff that goes out the door, the stuff that we can actually charge for, is what we want to do, so having a warehouse management system is great. Obviously, that was a big... By the way, I know there's certain warehouses, old ones, still don't even have that, but you're saying to really be as efficient and effective as you need to be in today's market, you need a warehouse execution system, that gets me the flow, gets me that throughput.
Yeah. I mean, it may not be for everybody, and there's certain things you can do where you can take a core WMS and just add some select capabilities from a full-blown WES, if only a modest or... I'll call it a modest level of that kind of automation is necessary, so it's not necessarily for everyone, and I don't want to position it that way, but it's certainly something that you'll want to take a look at.
Big boys need it.
Yeah, sometimes you get to where you've got a significant number of workers, but even smaller operations, things like the automated release of work to the floor without the human being needing to be involved, that's going to be attractive even for a midsize operation for sure.
So, first thing we need is we need to get into this... It's a WMS. That's a given. And you said there is incremental improvement for many years. Now you're starting to see big improvements, might even be driven by the market, that needed big improvements in recent years, and part of that is this WES. What else is there, part of that smart warehouse?
Yeah, there's a whole bunch of stuff. Let me just first, just as a reminder, the automation, because automation is... Obviously, that ties to the labor shortage, and even just a couple years ago, it was very common to talk to DC managers or logistics executives, and automation wasn't necessarily very high on their radar. Today, almost close to 100% of the companies we talk to, even smaller companies, are looking at automation of some kind. Now, that can be big automation, where you've got traditional sortation systems that can be very large, goods-to-person systems, those kind of things, but there's also a lot of interest in lighter, more flexible, and less expensive technology, things like what are called put walls, and a huge interest in automated and autonomous.
What’s a put wall?
Okay, so a put wall, in great simplicity, is a structure, a technique built on a structure, which is a module with a series of cubby holes or slots, and I could have one of these modules, I could have... We have one customer that has 80 of these modules, and what you do is you pick the orders, and then when you come to the put wall, you distribute the order, the picks excuse me, to the different orders that need that product.
So I batch pick the product. I bring it either mechanically or manually to the put wall, and typically a series of lights says, "Okay, this cubby hole number three here needs one of this SKU. Put one in. This one needs two of that SKU. Put two in. This one needs one. Put one in." That process repeats itself until all of the items for a given order are complete within that cubby hole, and then at that point, a... And that's called putting. That's why it's called a put wall. It's because you're picking the order in batch, then you're putting it into the put wall, and then around the backside, lights will turn on that indicate, "This cubby hole is now complete," and the operator comes up and touches a button typically, and that starts the printing of the label and any shipping documentation that's required, and the order is packed and shipped, and off you go.
It provides a tremendous amount of productivity, very flexible. You can start small. We had one customer that started with one put wall module, then added eight or nine more because they liked it, then they added 20 more because they really liked it. Did this all over a couple, three year type of period there. So for any kind of piece picking, especially of soft goods, but other types of products as well, but often driven by eCommerce, but not only by eCommerce, but any kind of heavy piece picking operation, put walls can be a great solution, but you've got to have the right software to do it.
So you've got that big, like almost a shelf, and you said like cubbies on that, that I push... So I'm putting product through it, so I've got to put... So maybe I walked over and I got 10 sweaters that are all the same, and this cubby gets one, this cubby gets one, and as I do that, I'm scanning it or it's recognizing that it's in there, and it's informing the other side of the cubby that-
When the order's complete.
When the order's complete, so maybe it needs two sweaters and a pair of shoes, and that's
That's correct.
The bottom line is we are entering a new era where all technologies are, in fact, much smarter than we've ever had before.
So that's just one more way. I mean, what do you call it? Is that part of... The technology is only part of it. The other piece of the cubby, the walking up to that, that's kind of... I could be putting those in bins in the old days, but this is putting that on steroids.
Yeah, it's just a new way of doing it, and there's a lot of... We'll talk about this actually, in terms of optimizing materials handling systems, because to get this right is not a trivial task, and I don't want to steal all my thunder from later on, but the ability to rapidly turn these put walls, these cubby holes, is the whole key to the success. If it's taking you a long time to do that, you're not getting the throughput that's required, and probably wasting your time and money. But if you can rapidly turn those by making sure the inventory gets there on time, and efficient execution at the wall, on both sides of the wall, then you've got something that really can drive a lot of productivity. We've got, I don't know what the number is, it's quite a few customers now that are using put walls, and when we go out to some new customers, we've got some videos that show them in operation, and you can tell they're just really, really interested in seeing how this works. I think it's the technology, along with the mobile robots, that you're just going to see any kind of eCommerce, but any kind of piece picking as well, you're going to see a lot of adoption going forward.
I can say this from... I'm an automotive guy originally. When you used to go through a plant, you would see people lifting heavy things when I first started, and crouching down, and doing functions that were hard on the body. And maybe it's not hard on them one day, or one week, or one month, but over one year, you're going to have a bad back, or bad shoulders, or bad knees. Same thing happens in these DCs, or the warehousing, so this automation you're talking about is making it easier on the workers, which means hopefully, I'll be able to keep my workers healthy and make that job, again, more attractive.
Yeah. Just quick anecdote, I one time talked to a VP of logistics at, I think it was Sherwin-Williams, the paint company, and he noted that on the manufacturing side of the operation, they were always having people retire and throwing retirement parties for them, with some cake and whatever. He said there was no one that ever retired from the distribution side, and that's because the heavy work of picking cases of paint is a young man's job, so as people got older, they just couldn't do that work anymore. So I think people are obviously rethinking that, for... The aging population is another factor, but how do I make the work easier so I can have somebody in their 50s and 60s continuing to do this distribution center job.
I think also, Dan, again I've said this once before on my... probably twice before on my podcast. If you gave me a choice to go work in an old-school warehouse or go deliver food or deliver groceries, I'm going to do the grocery delivery. I think I can make decent money, and I can sit in my car, and I don't have to hurt my back, or hurt my knees, or walk five miles a day. So we have to make these jobs more attractive, or we're not going to be able to keep and get good people.
Yeah. There's no question about that, and I think this automation that is of such interest, the jobs now, they've become more like a technician and less of an order picker.
I like it.
Yeah.
So besides a put wall, what's some other automation you're seeing out there?
Well, again, I said the automated mobile robots, autonomous mobile robots, or AMRs, there's a huge interest in that. One of the interesting things is that both put walls and mobile robots, you're seeing a lot of adoption and interest by third-party logistics companies, and I think this really just makes the point. In the past, 3PLs were very reluctant to do any kind of heavy automation, because they couldn't sync the return on investment with the contracts that they had from the shipper, so if the shipper... To pay off that equipment's going to take five, seven, whatever years, and the shipper's only going to give you a two- or three-year contract. The risk of automation is just too great.
Well, these other kind of systems, and that includes also things like voice, and pick-to-light smart cards, things like that. They're all kind of connected in some ways, but those kind of systems can be put in for much less expense, much lower risk, and again, be incrementally adapted. You can start with three mobile robots and see how you like it, and then add seven more later on or whatever, until you get to the optimal point for your operation. But the fact that 3PLs are making this kind of investment is a whole new phenomenon, and just speaks to the way you can incrementally get into the technology and the high-level payback that they're seeing, because we're very strong in the third-party logistics arena, just as an aside, so we're seeing it very closely, and the number of 3PLs that are interested in these kind of mid-range or lighter picking systems, not heavy automation, but other, it's often somewhat newer technologies, I think really just speaks to the changes we're seeing out there in the marketplace.
Yep. And by the way, those robots, depending on the facility, they're not necessarily always replacing people, because I talked to the guys from... I think it was the CEO or the president from DHL. He says, "Well, we thought we would be replacing people with robots." He goes, "The more robots we add to a facility, the more work we end up getting for that facility, and we end up hiring more people."
Yeah, and you know, it's just everyone has a shortage, right? So I mean, there's jobs going unfilled, so if the robots are taking some of that slack, if you will, but there are very few, if any, case studies of people adopting these technologies and they're still looking for people even after the automation, so-
[caption id="attachment_7942" align="aligncenter" width="600"] The Smart Warehouse: WES (Warehouse Execution System) will help manage the flow of work and resource utilization.[/caption]
Yep. So what's another thing we need for that smart warehouse, Dan?
Well, I mean now let's just kind of get into it in some more detail. Really, and we talked about some of the core software components if you will, things like warehouse management systems, warehouse execution systems, but a platform for integrating these automation, both heavy and... or traditional and newer-age capabilities. We'll talk about that in just a second, and then there's some enabling technologies, things like rules engines, and a simulation, and some other things, so we'll talk about that, but I like to say the core warehouse operations excellence is still the foundation, right? So how do I get that right? That typically involves traditional WMS-type capabilities. What does that mean? Well, I mean what kind of defines a warehouse management system versus an inventory system is the pervasive use of mobile terminals, and barcode scanning, wireless RF devices, or whatever term you want to use there.
And then a lot of system-directed activity, and this whole notion of task management and task monitoring, where the system kind of is orchestrating the different traditional tasks of put away, receiving put away, picking, replenishment, et cetera, and support for multiple strategies around that. I want to have lots of different picking method options, and want to have lots of different replenishment strategies that I can use. And then you know, things that have been around for a while, like slotting optimization, and detailed labor management, labor reporting, things like that.
So the foundation really is core operations excellence. That's what everyone should strive to get to, but today, there's now ability to take that even further in terms of different types of capabilities that we think are defining what we're calling the smart warehouse.
Yep, and you used a term there, that was integration platform. What am I integrating?
Yeah, you're integrating primarily different materials handling technologies. That can be things we've had for a while, like conveyor transport and sortation. It can be some of these newer technologies, like robots and put walls. But the key really is, and again, we'll talk about this in just a second here, but the key really is how do I optimize the flow, so I don't have these islands of automation that are all doing their own thing? I recently talked to somebody in the apparel industry, and they have a very large and highly automated facility, I think somewhere down in the Atlanta area, like a million or two million square feet, and they're seeing their throughput from that building, after huge investments over years, certainly initially and then over time.
They're seeing the throughput actually decline, and what's happening, he believed, is that business keeps changing. They keep having all these new requirements in terms of how an order needs to be processed, and what they do is they just keep building new wave types. We talked about wave planning before, and now they're up to like 70, 80 different wave types, and every time there's another problem, create wave type number 82, see if that solves our problem. That's not solving the problem, and part of the reason is because the system is not looking holistically across the facility, and seeing how I can optimize the flow of work as a whole, not as an individual subsystem. I think that's really part of what we're talking about here with the smart warehouse, and that's the kind of thing that traditional WMSs have not done.
Yeah, so that integration platform, that means I can connect all my... So all the tools, all the different systems I'm using, all connect easily through that integration, as opposed to the old way, which is a standalone, $100,000 integration with expensive people who have to code.
Yeah. That's certainly part of it, and then it's managing the flow of work across that. I'm maybe getting ahead of myself again here, but I'll just say for example, you can have some scenarios where I have different paths for an order to be fulfilled. One of the paths, and the most efficient for certain kinds of orders, is in fact maybe a group of put wall modules. But let's say that that put wall area, for whatever reason, starts to be congested, and all of a sudden now there's a big backup on the conveyor feeding into the put wall area. Well, the system is going to automatically recognize that, and for some period of time, route orders away from the put wall into manual cart picking, which takes them to the packing station, same packing area where the put wall [inaudible 00:33:11] leads. And then when the congestion is clear, then the system automatically reroutes that work back to the put walls again. So now you're looking not only at the plain integration, but actually in monitoring the flow of work that's happening and making realtime decisions accordingly.
Yep. You know, I'm an automotive guy, and we had all of those years where we started... We used the term "smart factories," and it was just the same thing, how do we increase throughput? Because what can happen is you can end up with a local optimum, where some guys are building a big, big stack of inventory, and does nobody any good. What is all that excess inventory doing for me, right? What makes more sense is to say, "We're going to get this so there's a flow to it, and we're not building up too much inventory. There's no bottlenecks." I think this is kind of the same thing you're talking about here, is how do I arrange my people so I don't have these guys sitting around because they already finished, while these guys are, to your point, congested area?
The core world’s operations excellence is still the foundation.
No, and that's really... The term flow manufacturing came out of exactly what you're talking about there, and was largely developed, initially, in the automotive industry, so we're talking about the same thing, and now we're talking about flow distribution instead of flow manufacturing, but the fundamental concepts, more of a pull-based system, more being aware of capacities and constraints, more concerned with the total flow of goods, not what's happening at one individual area. All those are very consistent, whether you're looking... The principles that were established earlier in manufacturing are what's being applied here today in distribution.
Right, and I'm just going to assume that at one time, the WMS, a big selling point would be, "We'll tell you where your inventory is at," and that was probably a big step up, right? But today you go, "Of course it does that. Now I'm going to tell you how that inventory moves off of your shelves and out the door, and how you bring new inventory in."
Yeah. It's amazing. We still see quite a few... I mean, every week we see somebody that's calling or emailing in, and then we talk to them, and it turns out they don't have that realtime visibility to inventory, because they're using some kind of paper-based system or something, so it's amazing, and sometimes these are even good-sized companies. But in general, yes you are right. Certainly anybody that's implemented any kind of tier one, or tier two level even, WMS should be having that realtime inventory visibility, and doing that, and that gets into that operations excellence I'm talking about. That's the foundation, right? I've got to know what I got, and where it is by lot, by batch, by serial number, by whatever attribute is important for your operation, or combination of attributes, or whatever. That's the foundation, but now we're saying, "Okay, how do we optimize on top of that, to just get more product out the door at a lower cost?"
Yeah, it requires investment. I mean, having a WMS tells me, "Here's information," but it's not enough anymore, to your point, is we need all of this to get there.
Yeah, and that's where kind of... You asked me about some of the components of the smart warehouse, and I talked about it from a kind of a product category perspective, but now I'm talking about it more from a almost philosophical and one of the things is one of the key foundations I that constraining condition awareness. What's happening in my building? What's happening with the flow of goods? One of the things that first really got me to understand WES in a deeper way is this notion that it's always on, listening and monitoring the environment. If you think about a traditional WMS, it's more sequential oriented. I receive product in, I put it away. I replenish pick sites. I do the picking. I take it to packing or value-added services. I put it in the receiving staging or shipping staging. I get it out the door. All very good, and a lot of companies don't have that, and organizing all of that, and automating, if you will, that is a big step forward.
But we need to take it to the next level, so if you think about this notion of the system is always on, monitoring throughput and flow, so there's certain rates and certain throughput that I'm expecting, so I need to be able to have a flexible set of dashboards supported by event alerts and notifications that there is a problem, that says, "Here's what's happening across..." However I want to define it in that area, I can define an area as a case picking modules, as a whole three-level case pick module. I see that as one unit, and I want to know what the throughput is there. Maybe I want to see it at each level of that pick module, so I can see it more granularly.
What's really nifty about this is that that new level of visibility to activity, and throughput, and bottlenecks, and alerts, and corrective action, automated, increasingly automated, if there are bottlenecks, but that provides a nice set of realtime dashboards, and really cool-looking stuff that people can see what's happening, "I have this many orders pending. Here's how many have been completed, or here's how many are in picking," or all of that kind of real level of detail.
But to understanding what's going on here with the smart warehouse is the system is using that same data that's being exposed to managers and supervisors. That's what it's using to make decisions as well, and I cited that example of being aware of the backup that's happening in the put wall, and automatically for some period of time routing work around that until the congestion is cleared. That's what's really kind of different now about this kind of visibility and this kind of activity monitoring, and being able to flexibly do that at however you want to, again, define. Processing area could be evaluated, services, it could be piece picking. You know, all these things, and obviously now the design is that these different flows throughout the facility are in sync, okay?
I'm not getting all backed up in packing, which is causing problems way back in picking and replenishment, because I haven't automated the visibility and I haven't automated the flow release in a way that's going to be cognizant and aware that I've got a problem here, and here's what I need to do about it for some period of time until it corrects itself, or suggesting, or just taking action, to solve the problem.
You know what? You sent me a PowerPoint, and I have this up here, and it's got that realtime, configurable dashboards, and one of the things that always drives me crazy going to warehouses... Well, it's been a while since I've seen somebody hand me a piece of paper, but somebody handed me a piece of paper that had like 40 columns, and it was like an Excel spreadsheet or something. It maybe have spit out of a system, I don't know. But it had so much, and I looked at it. I was like, "What am I supposed to do with this?" I like the idea of being able to configure it for those KPIs that I care about. I don't want to measure everything. That's just me. Tell me the four, or five, or seven things that really matter, that tell me my warehouse is moving in the right direction, that things are working well. I see also, I'm just looking at it in here, it says, "Orders with issues." I also love the idea that I don't find out about the issues in next week's report. I find out about them real time.
[caption id="attachment_7943" align="aligncenter" width="600"] The Smart Warehouse: One of the things that got me to understand WES in a deeper way is this notion that it's always on, listening and monitoring the environment.[/caption]
Yeah, that's absolutely true, and then the point that you made actually, kind of a nice transition to this notion of another component we talked about, the realtime visibility to capacities, and constraints, and conditions out there, and then the always on nature of the WES, but now, also we talked about looking at a table of 40 rows of information or whatever, and what do I do.
And it's all in the past, too.
It's in the past, but I think it brings up a point there, which is today, even with higher-end WMSs, this is one of the learnings and insights that we have, there is still a tremendous amount of decision-making that is being done by human beings, so just as the manager or whoever you were talking about there in your example, staring at a 40-row spreadsheet or whatever, you see the same thing today, of managers and supervisors staring at computer screens, trying to figure out what the right thing to do is next. Here's the reality. Every time you do that, first off, you introduce some latency into the system, because it takes time to look at the different screens, and to think about it, and to make decisions, and scribble some things down on a piece of paper to remind you this needs to be taken care of or whatever, okay?
And then simply, in most cases, there's no way a human being can make the optimal decision in the same way that a computer can, because even if you're a really smart guy or gal, there's just too much data, too much to try to process at one time. So part of the capabilities of the smart WMS is the much more advanced software-based decision-making, so things like order batch optimization. Given a given block of work, what's the best way to most effectively execute that out on the software floor? What we think is absolutely huge is this notion of the autonomous warehouse. That's a term Gartner has used, others have used it as well, but it talks about being able to automatically release work, without the need for a wave planner, or inventory expediters, or all the kind of people that you see often involved in these kind of decisions about what work to do when.
So work is really sort of attributes, things like the order priority, the inventory and resource availability, what kind of optimization opportunities are there, you know? The bigger the order pool, the more optimization opportunities you have, because there are just more data to be optimized, conditions to be optimized, but also you've got... but you can't hold on so long that you're not getting the throughput out the door. Courier cutoff time, this is a huge one. I mean, even in sophisticated warehouses today, at 4:00 or 5:00, when the UPS or the FedEx or whatever truck is leaving, you often see... And we've made commitments that eCommerce is going to ship today. You see a certain amount of chaos going around, trying to figure out if all the orders that need to go on that truck have been on the truck and what to do about it.
What we're talking about here, we're saying, "Okay, listen. We know this is the work. We know how long it's going to take to pick and transport that work, those orders, to the shipping dock or whatever," so the work is going to automatically release itself at the beginning of the day. We're more concerned about optimization. We've still got a lot of decent amount of time, so we can focus on doing it the most efficient we can, but as you go throughout the day, that needle starts to change from the focus on efficiency on cost to efficiency on customer service, and making sure those items are on there. And the system just does that automatically. It's configured to take those into consideration. So now those orders are getting on the trucks automatically, without the chaos, and without just the difficulty that's going on out there.
This is just a whole new... This is step change capability here. I mean, we're talking about a system that's kind of self-learning and optimal how it releases work, and this is just not a concept we've had in distribution software before, and this is what really defines what we're calling the smart warehouse.
Yeah, and it's interesting. I had a boss in the past, when I was young, and I remember I sent an Excel spreadsheet to him, and it told a story. I sent it to him, and he pulled me into his office, he says, "Joe, this is a great Excel spreadsheet." He says, "So I have to go through here and I have to come to the same conclusion you did," and I go, "Well, that's easy. You just look at the..." And he goes, "No, no, no." He goes, "When you send me this Excel spreadsheet, send me a recommendation. I don't want to have to come to a conclusion. That's your job. You could attach the data as backup, but give me a recommendation," and I feel the same way about running a warehouse. Don't make me figure it out myself. Give me an alert that says, "This is a problem." Say, "This is how many orders are at risk," right? "This is how many orders need to get on that truck that aren't done yet." Give me that.
And just to show you, as a simple example, still a lot of people, especially for eCommerce, are doing manual cart picking, so I may have a cart that's got a certain configuration, three by three or four by four... What I mean by that, three by three would be three shelves that each have room for three cartons each, right? So I have nine total orders that I'm working on there. Well, most companies that we see do that today, they're doing it with paper picking, or pick by label, or something. There's some attempt to do that more efficiently, but just something as simple as cart picking. The smart warehouse can take it to a whole new level, so first off, you've got again, as I said, this order pool that's out there, and at any one point of time, and now I'm probably going to have done some cartonization logic there to determine what should go in what box, especially with a multi-carton order.
In most cases, there’s no way a human being can make the optimal decision in the same way that a computer can. Even if you’re really smart, there’s just too much data to process at one time.
If you're shipping, just for example, you don't want to put perfume in the same carton as apparel, because of the obvious contamination that can happen there. But now somebody comes up, a picker comes up, and scans a barcode on that cart. The system's going to automatically know it's this configuration, three by three, four by four, whatever, and it will have done some optimization, typically in terms of what's called cluster picking, where I'm going to take that cart to one location, and then I will have put as many orders as I can on the cart, assigned to that cart, that have the same set of SKUs on them, so I can minimize my travel distance. Hopefully, I'm being clear on what that means.
So now I get to that location that says... And this can be done with lights or it can be done with barcode scanning. It says, "Okay, take one of these from this location, put it in carton slot three one," which is the third shelf, the first location. The next one is three two, the next one is two three, the next one is two one, whatever that sequence is, right? So I'm doing that in a way that makes it very, very efficient. But we could take it even still beyond that.
What if a high-priority order comes on? The picker is walking along. As long as there's a location on that cart, whether it's a carton or a tote they're picking into, if it hasn't been started, we can remove, automatically, a lower-priority order and insert a higher-priority order that has just come down onto that cart, as long as... We typically do it so the picker doesn't have to turn around and go backwards. As long as the picks for the new order are ahead of that picker, okay? And we do that without the picker even being aware that it happened.
Yeah, so you can kind of expedite, automatically, like, "Hey, I got a truck that's going to be here in an hour and we haven't even started yet. Let's get this going."
Yeah, or just maybe a customer... We say if you get an order in by 2:00, we'll ship it that day, and it's 1:58, and all of a sudden, an order just drops, right? I got two minutes, you know? Or whatever to do that, so the system's going to automatically insert a higher-priority order where possible.
I like something you said in there, that we talked about the labor problem with these guys walking around maybe five, 10 miles in a day, and one of the reasons we're going to quit, especially if you're me. I don't want to walk that many steps. If you can optimize, so when I walk over there, all my orders are in the same area. Then I walk over here, and all my orders are there, as opposed to one order on one side of the warehouse, another order on the other side, where I'm walking and going, "What the hell has my life become, where I walk back and forth like this?"
Yeah.
Costly too.
That gets into the order pool optimization as well, because the bigger the batch that I'm working with, the more opportunities I have to gang those picks together, so on a given cart, I'm maybe walking very few feet. And then, just to your point, this is where you get into the whole notion of mobile robots and whatnot too, because now perhaps I go to the pick location, I pick the order, but instead of putting it on a pick cart, I'm putting it on a mobile robot, and the mobile robot's going to move onto the next location, or onto packing if the order's complete, or whatever, so I'm walking very little at that point, or comparatively little, which is obviously one of the attractivenesses of the mobile robot technologies. Again, so this is hopefully it's becoming clear here. This is the nature of the warehouse is changing, and part of that's going to have to be to not only be more cost efficient and get more out the door with the staff that I've got, but it's making sure the people have a less miserable work experience, and hence hopefully are going to stay with us a lot longer.
Man, this is not your grandpa's warehouse anymore, and I think to be competitive... It used to be like, "Wow, these guys are high tech because they have a WMS," and now we're starting to spin out the automation, and the warehouse execution, and the integration platform. This is all getting really high tech, and you think this was probably the lowest-tech business there was 25 years ago.
Yeah. I mean, it's just inevitable, and how is that all going to play out? It's going to be interesting to see, but again, I think the lighter automation techniques, including the robots and the put walls, are just so attractive in terms of their flexibility and expandability, and now when you add... And there's, we'll maybe talk about it a little bit about this, but there's machine learning and artificial intelligence, all kind of things going into... involved here, so yes, the warehouses are becoming technology centers, and if you see the kind of private equity money that's flowing into robotics firms, and AI firms, and others, obviously a lot of the smart money thinks that's where it's headed too.
Well, and also I think companies are starting to realize, retailers and other eCommerce companies, are starting to realize the importance of a real well-run warehouse. What's those guys, Quiet Logistics? They got bought by American Eagle. That was American Eagle recognizing, another traditional retailer, saying, "We're going to buy ourselves a warehousing company, because that's how important this business is."
Yeah, and of course, Quiet was actually the force behind what has become Locus Robots, one of the big mobile robot vendors. That happened because Amazon had bought Kiva Systems right before that, and kind of left Quiet without a partner, they were building the business on, so they went out and invented their own robots, so yeah.
[caption id="attachment_7944" align="aligncenter" width="600"] The Smart Warehouse: What's really different now about this kind of visibility and activity monitoring is being able to flexibly do that however you want to define a processing area.[/caption]
Yeah, that's right. Bruce Welty was on my podcast. He's the founder of Quiet, and he said... I don't know when, a long time ago, he got a phone call saying, "Hey, you guys using those Locus Robots?" And he says, "Yeah. How do you like them?" "We like them a lot." And they said, "Can we come visit?" "Sure." It was Amazon. Amazon looked around, said, "We love this." They bought Locus, and then they stopped supporting... Or no, that was the other one. Or was that Kiva? I'm taking it back. That was Kiva.
A couple of other things I'd like to just bring up about the smart warehouse. As much as broader use of some auto-ID-ish, or IoT-type devices. RFID is starting to make something of a comeback, years after the Walmart debacle in 2003, or 2004, or whatever, but certainly there is, I think, you're going to see many manual scanning activities that are going to disappear as RFID moves its way back now, from being implemented at the store level by customers concerned with eCommerce fulfillment, for inventory purposes. You're going to see it move back up into the distribution operations, so I think that will certainly be part of it. IoT, I mean, we're already doing things today, like for example, we're partnered with a pick cart.
That's internet of things.
Yeah, correct, obviously. A picker with a pick cart can walk up to a pick zone, and the IoT automatically recognizes it's this cart with this person on it, so it automatically turns on the lights, the pick lights that are on those four pick locations. It's a minor thing there, but that's just the kind of advancement we're going to see, and we've even done some stuff with kind of congestion management, and COVID or whatever, where we can actually tell exactly where somebody is in the aisle using IoT, and being able to assign work based on a realtime visibility to who's actually closest to that work, but also in a COVID area, being able to space people apart so that they don't get, say, within eight feet of each other, or whatever how that happens to be, whatever metric you want it to do, to use there for that, or constraint. So there's some very interesting things that can happen there. You know, this is still kind of slow-going. It hasn't taken off as fast as many people think, but I think you're going to see RFID and IoT start to make some real inroads over the next three years or so.
Then, we have this notion, or follow the notion of Gartner on what's considered to be called conversational voice, so transactional voice is doing a picking or a palette build or something using voice technologies, and typically reading in a check location, check digit, and some of those kind of things, and doing a hands-free pick, or replenishment, or whatever the task might be, but we're starting to get now into more of a dialogue, so we're already to the point now where we can have a supervisor take a smart phone and say, "Hey, show me how I'm doing on wave number 235," or whatever, and then over a smart phone, that's going to bring back exactly what's happening now, or, "Where's our replenishment for location 3652," or whatever.
So we're still early in this game here, but certainly we'll move to more of a dialogue going on with the WMS and WES than just plain transactional voice type technology. We think this is very exciting, and where the future interface of the software is going to really head.
Yep, and this is where that integration platform you talked about comes in handy, so I can connect to all this stuff. The new killer app that comes out, I can get it.
Yeah, and you know, we've done a lot there, so automation and optimization of materials handling systems is certainly a key part of this. I mean, we really refer to it not just as the smart warehouse of the future, but actually the smart automated warehouse of the future, due to the interest in the technologies we've talked about several times already today, so we can directly connect with these picking subsystems, like walls, like pick-to-light, like voice, like whatever, without the need for third-party software. Everyone else uses some kind of software from the put wall vendor, or from the pick-to-light vendor, or from the voice vendor, or whatever. Adds another layer of integration, adds another layer of cost, and it often results in people operating in kind of silos. We can directly control a lot of these materials handling technologies, and it allows you to operate those and optimize those in the context of everything that's happening in the warehouse, and all the information that's available, which just provides you a lot of benefits over time, because again, you're not just trying to operate in silos.
I talked to somebody that was using a pick-to-light system the other day, a couple months ago I guess, and they talked about how at the end of every week, they've got to go in and clean up all these picks that somehow never happened, never were executed in the pick-to-light system, and, "I'm not quite sure why that is," but it just wouldn't happen with the way we're approaching things, because we would be aware of that. It probably is waiting on a replenishment or whatever. The problem is, the pick-to-light vendor doesn't do replenishment. The WMS vendor does it.
So you've got these kind of silos going on here, and there's a lot of opportunities, and in terms of that integration platform, we think this is especially true for mobile robots. People are using the mobile software of the mobile robots, but what that does is it limits, again, sort of the total optimization that can be achieved, but more importantly, you're now totally dependent on that robot software, and what if you want to add different robots? Or what if you want to change horses three years from now? Or there's a better mouse trap, or faster, or whatever that happens to be. Now you can become locked in, so what we think the market really needs is a mobile robot and broader automation integration platform, almost like an operating system for automation in the warehouse, that's going to allow you to have visibility to and optimization of robots of different kinds from the same manufacturer, of different types for different manufacturers, so you're not locked in. It's like a plug-and-play type environment here.
We refer to it not just as smart but the smart automated across to the future.
Three years from now, you can keep the robots you have if you want, keep the 10 that you bought, but now you want to add five more from a different vendor. Plug them into this operating system, and have instant connectivity and the ability to optimize for performance. We just think that's the much more low-risk approach going forward than locking yourself into a vendor today, the software that's coming from the robot vendor.
Yeah, and I think, let me get back to the idea of a smart warehouse, it's all about throughput. If I have different systems, that are connecting, that are doing local optimums, that's a problem, because it's not supporting throughput. So I always need that one... I'll call it the one source of truth. That's the main system, to say, "This is all about getting stuff out the door here," and so-
Yeah, I wanted to bring up just one... I think earlier in the broadcast, I talked about wanting to give an example with the put wall. We've talked about put walls several times now, but again, I referenced that the whole key is to turning over those put walls. Well, here's the kind of scenario that... The cubby holes in the put walls. Here's the kind of scenario we're seeing, where let's say there's a three line item eCommerce order, and two of those line items on the order come from a cart and flow rack area that's very close to packing. I mean, those orders are efficient to pick and short distance to transport.
If you don't do anything else, and the third line item is actually coming from a slow-moving mezzanine pick area, that's farther away and is less efficient to pick. If you don't do anything otherwise, what's going to happen is those first two items from that order are going to show up rather quickly, and then they're going to sit, and wait, and wait, and wait, and they're going to wait 10 minutes, 15 minutes, 20 minutes, 45 minutes, whatever it happens to be, for that third item on the order to finally show up. That cubby hole's been tied up that entire time. What's the smarter warehouse way of doing it? What's the WES way of doing it?
It would be to recognize that difference. Let's say it's 25% slower to go through the mezzanine or whatever the number you want to use is. We would release just that third line item in effect 25 or 30% earlier, and then after the time it takes to pick and transport that, as it's on its way to the pack station, now we release the other two orders, line items, just for the cart and flow rack, so voila, they show up at the put wall for processing at relatively the same time, and now I'm able to turn that wall without the latency that would occur if you didn't have smart software to do that. So hopefully that's an example that makes it somewhat clearer as to how the optimization really can affect operational performance.
You would never be able to get that done manually. Just doesn't happen. Man, this is like drinking from a firehouse. This is so much going on in this. So, Dan, put a bow on this bad boy. Give us your final thoughts on this. What do I need to get to have that smart warehouse?
Yeah, well I mean, first off, it provides a ton of benefits. It's going to reduce labor costs. You're going to have higher and more consistent DC throughput. You're going to reduce your need for automation, in terms of things like the number of diverts, or get more throughput out of the automation you have there. We didn't talk much about labor planning today, but that's a big part of it. You can dynamically assign workers throughout the course of a shift, from one hour, 8:00 to 9:00, 9:00 to 10:00, 10:00 to 11:00, wherever they're needed most and in what quantities. Improved automated decision-making, we talked about all that. So you know, it's really just an assessment, and certainly if you're heavily automated, there's a lot of opportunities for you, but as I tried to make the point earlier, even if you're only modestly automated or not automated at all, these things, these capabilities can have some real benefit for your operations.
I think the important thing to note, related to Softeon, is these can be implemented very incrementally. I could implement a traditional WMS, and let's say I just want the labor planning and allocation part of it, as I just talked about a second ago. We can take that capability from WES and just, if you will, attach it to the WMS, to give you a solution. Conversely, if you want to implement WES and leave your existing WMS in place, we didn't talk much about that today, but that's a key dynamic. But you need cartonization, which is a warehouse management function. You can just attach, if you will, cartonization to that WES implementation, so flexibility is key. That's what we try to design. We call it a share component library, that the applications can borrow components, and functionality, and services from each other, and we're pretty confident that give us a chance to understand what you're trying to accomplish, and what your operation's like, or whatever, that some combination of these technologies are going to have a pretty good fit and really take your warehouse to a whole new level than we've seen over the last 20 years.
Excellent, excellent. Well, man, it has changed a lot. Dan, what's new over at Softeon? What conferences you guys going to? What's new over at-
Yeah, so we just got done with the MODEX show a few weeks ago, and it was a big success for us. We not only showed the smart warehouse, kind of presented the smart warehouse capabilities. We actually had a lot of equipment, pick wall, pick-to-light, other technology, packing stations, et cetera, right in our booth, and at the bottom of every hour, we did a presentation, had consistently good traffic the whole time, and then we actually did a... They have an educational track. We actually did a session on the smart warehouse of the future, available on Softeon today. It was very well attended, so that was good. We'll be at the Gartner Supply Chain Symposium. I think it's early June, down in Orlando, and then kind of a break after that, but we just finished up a series of broadcasts, educational broadcasts, called The WMS Bootcamp, six different sessions from everything from building the business case to how to implement successfully.
[caption id="attachment_7945" align="aligncenter" width="600"] The Smart Warehouse: Even if you're just modestly automated, these capabilities can have some real benefits on your operations. These can be implemented very incrementally.[/caption]
It was a huge success, but all that's now available on demand. If they go onto softeon.com, you'll be able to find some links to that, and I think if you have any interest in WMS any time soon, or even mid term, this will be... They're noncommercial educational sessions. I think you'll find they add a lot of value. The feedback we got on it was outstanding.
Dan, what I'll do is I'll put a link to those. If you give me the link to those WMS Bootcamp, I would like to watch it myself, because I think this... We just went over this, and it has gone from simple to just more complex over time, and you know, you guys are simplifying it, but to understand what's required requires a bootcamp.
Well, there's just a lot of... We wrote a lot of lessons over time, and I brought in some consultants and people that I knew really knew what they were talking about, in terms of like building the business case. We had some folks from Invista that came on and did that, and I just had some experience there, exposure, I knew they knew what they were talking about. I assume that applies to some other consultants as well, so it's a real nice series. It's noncommercial. If you want to learn some tips about how to get WMS selection and implementation right, I think you'll find the bootcamp serves you well.
How do we reach out and talk to you over at Softeon?
Yeah, easiest way to get to me is just via email. My email address is just [email protected]. You can also use [email protected] for just the general inquiry box, but love to hear from you. Hopefully came across that I at least know a little bit about what I'm talking about, and I'd love to discuss your problems as well.
Yep. And what I'll do is I'll put a link to your LinkedIn profile and also a link to Softeon's website, and anyone who wants to reach out can reach out and talk to you about the smart warehouse.
Thanks, Joe. I really enjoyed it. It was a great conversation. Thank you.
Thank you so much, Dan, and thank all of you for listening to my podcast. Your support's very much appreciated. Until next time, onward and upward.
Important Links
- Softeon
- Supply Chain Digest
- WMS Bootcamp
- [email protected]
- [email protected]
- https://www.linkedin.com/company/softeon