We can't find the internet
Attempting to reconnect
Something went wrong!
Hang in there while we get back on track
Ep 68 – Deming’s Red Bead Experiment
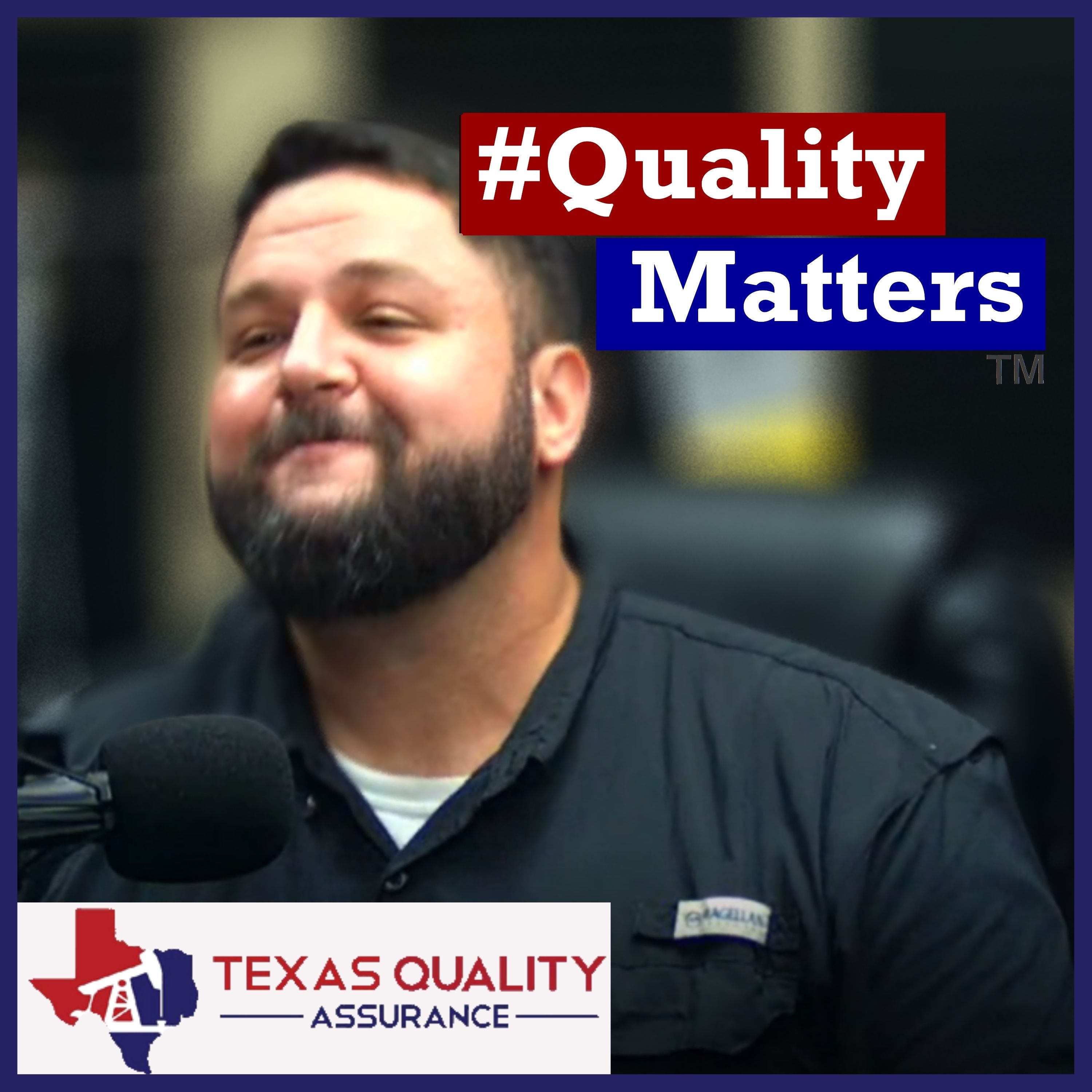
Access AI content by logging in
Who hasn’t heard of Deming’s Red Bead Experiment? A lot of people, probably. However, if you’ve ever worked somewhere that you’ve done your best, followed the procedures, and your performance still wasn’t good, you may be trapped in a red bead system. This episode shows us how important a system is that includes opportunity for employees to offer input on continual improvement.
Deming, in a workshop, “hires” a few employees. Their job is to fill a small paddle with all white beads. The workers will dip the paddle into a box that is comprised of 3200 white beads and 800 red. Deming gives specific instructions to work within his well-defined system on how to hold the paddle, scoop the beads, gently agitate the paddle to release excess beads, take the paddle to the 2 inspectors for inspection and recording. Deming then fires a few of the not so good employees, and keeps his best workers on with new requirements, lowering the number of red beads allowed. Of course, the best workers performance is really left to chance and there are more firings.
The idea is that no matter how well defined your system is, there must be room for change. Employees were not allowed to suggest improvements, look for defects in the incoming supply and the system had nothing to do with the employee’s capabilities.
In the red bead experiment, employees were blamed for their poor performance and the bead company goes out of business. Companies need to have a system set up that supports their employees suggesting continual improvement.
https://blog.deming.org/2014/03/lessons-from-the-red-bead-experiment-with-dr-deming/
https://youtu.be/HmCjr6cwDpI
Learn more about #QualityMatters & Texas Quality Assurance :LinkedIn | Facebook | Twitter | Instagram | YouTubewww.qmcast.com | Texas Quality Assurance